Zu den neuen Fertigungsverfahren aus dem Projekt Zyklomed haben wir schnell Anfragen bekommen, eine sogar aus Schweden“, berichtet Dr. Matthias Luik, keine zwei Wochen nach den Technologietagen bei der Paul Horn GmbH in Tübingen. „Damit hatten wir gar nicht gerechnet“, sagt der Entwicklungsleiter – aber dass er das Interesse am Rotationsunrunddrehen, dem Polygondrehen und dem High-Speed-Wirbelfräsen (Dreh-Wirbelfräsen) erfreulich findet, merkt man ihm an. Mit diesen Verfahren lassen sich Knochennägel und Knochenschrauben aus Titan schneller und damit wirtschaftlicher herstellen. Darüber haben bei den Technologietagen die vier Partner aus dem Projekt Zyklomed genauer berichtet – und hatten so für Medizinprodukte-Hersteller eine Besonderheit zu bieten.
Knochenplatte zeigt, was bei der Titanbearbeitung möglich ist
Im Projekt ging es darum, wie sich moderne Designs medizinischer Implantate für Orthopädie, Traumatologie und Dentaltechnik wirtschaftlich herstellen lassen. Die multifunktionalen sowie unrund-bionischen Formen werden bisher in mehreren Schritten auf verschiedenen Maschinen gefertigt. Das dauert, und jedes Umspannen steigert die Kosten, wenn kein Verlust an Genauigkeit auftreten soll.
Vier Zyklomed-Partner tasten sich an neue Verfahren heran
Mit dem Rotationsunrunddrehen, Polygondrehen und High-Speed-Wirbelfräsen soll sich das verbessern. Wie genau, daran haben der Drehmaschinenhersteller Index Werke GmbH & Co KG Hahn & Tessky aus Esslingen, der Werkzeugspezialist Paul Horn GmbH und die Beutter Präzisions-Komponenten GmbH & Co. KG zusammengearbeitet. Beutter stellt als Zulieferer feinmechanische Komponenten her, auch für die Medizintechnik. Als vierter Partner im vom Bundesministerium für Bildung und Forschung (BMBF) geförderten Projekt war das WBK Institut für Produktionstechnik am Karlsruher Institut für Technologie (KIT) mit im Boot. „Zu dem, was wir da vorhatten und am Beispiel von Knochennagel und Knochenschraube zeigen wollten, gab es ja noch keine Erfahrungen“, sagt Luik. „Wir mussten uns herantasten. Für das Design der Werkzeuge zum Beispiel waren Simulationsdaten aus Karlsruhe sehr hilfreich.“
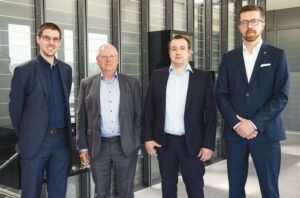
(Bild: Horn/Sauermann)
Titan bearbeiten und zu anspruchsvollen Formen kommen
Um geschwungene Flächen und Funktionselemente mit kontinuierlichen Übergängen auf kleinstem Raum herzustellen, setzen die Projektpartner auf das kinematische Prinzip mehrerer synchronisiert rotierender Achsen. Dieses ist an sich altbekannt. Doch war die Anwendung auf unrunde und geschwungene Formen „hochgradig anspruchsvoll“, wie es Andreas Kanz beschreibt. Er hat das Projekt als Mitarbeiter im Bereich Entwicklung bei Paul Horn begleitet. „Wir wollten und mussten in der praktischen Umsetzung ja auch die hohen Qualitätsanforderungen der Medizintechnik erfüllen.“
Sehr filigrane Werkzeugstrukturen erforderlich
Das ist gelungen, wie Versuche im seriennahen Umfeld zeigen. „Es war aber nicht immer so klar“, räumt Entwicklungsleiter Luik ein. Angesichts der Simulationen mit sehr filigranen Werkzeugstrukturen hätte sein Bauchgefühl eher Zweifel signalisiert. „Wir mussten auch Lehrgeld bezahlen. Aber heute haben wir für die Prozesse ein gutes Gespür.“
Auch wenn das Projekt noch nicht abgeschlossen sei, zeigten die Tests gute Ergebnisse bei den Oberflächen und zur Standzeit der Werkzeuge. „Wir haben es geschafft, mit demselben Werkzeug 500 Schraubenanschlüsse aus Titan zu bearbeiten.“ Und er nennt Beispiele für die Geschwindigkeit: Eine Torx-ähnliche Struktur ließ sich im Test in nur 13 s herstellen. Für einen Knochennagel mit unrundem Profil brauchte es 2 min – wobei der Vergleichswert, der mit konventioneller Bearbeitung erreicht wird, bei 15 min liegt.
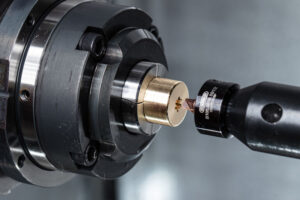
(Bild: Horn/Sauermann)
Weitere Versuche laufen noch bis zum Herbst, um die Werte unter Praxisbedingungen im industriellen Einsatz zu prüfen und zu untermauern. Lieferbar sind die verwendeten Werkzeuge daher noch nicht alle – sondern erst, sobald belastbare Daten zu den Standzeiten vorliegen. „Wenn wir konkrete Anfragen bekommen, prüfen wir diese und verweisen gegebenenfalls auf das dritte Quartal 2023“, so Dr. Luik.
Schnell, wirtschaftlich – und auch neue Formen sind möglich
Den Interessenten geht es aber nicht nur darum, die komplexen Geometrien schneller und besonders wirtschaftlich allein mit einer Drehmaschine herzustellen. „Was auch zählt, ist, dass sich so neue Formen fertigen lassen“, sagt der Entwicklungsleiter. Dazu zählen zum Beispiel zwei- oder sogar dreigängige Gewinde, die sich mit einem Werkzeug herstellen lassen – oder Gewinde mit echter variabler Steigung, deren Gewindeprofil sich also dynamisch ändert. Eine weitere Idee: „Wir gehen davon aus, dass wir auch unrunde Instrumentengriffe so herstellen können“, führt Luik aus.
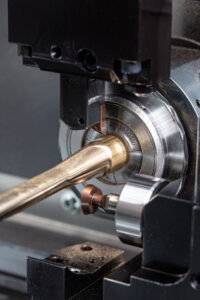
(Bild: Horn/Sauermann)
Trotz der Vorteile bei Geschwindigkeit und Formgebung ist der Umstieg auf eines der neuen Verfahren nicht immer sofort möglich. „Das ist keine Plug&Play-Lösung“, sagt Luik und empfiehlt im Vorfeld eine Prüfung für den konkreten Anwendungsfall – wofür die Spezialisten von Horn gern zur Verfügung stehen. Besonders beim Rotationsunrunddrehen sei darauf zu achten, dass beispielsweise die Parameter so gut gewählt sind, dass sich der Span nicht um das Bauteil wickelt. Ebenfalls wichtig sei, dass Werkzeuge für das Polygondrehen und das High-Speed-Wirbelfräsen jeweils produktspezifisch angepasst sein müssen.
Achsen in der Maschine müssen 100 Prozent synchron laufen
„Eine sehr wichtige Voraussetzung ist auch, dass die Achsen in der verwendeten Maschine zu hundert Prozent synchron laufen“, ergänzt Entwicklungsingenieur und Zyklomed-Experte Kanz. Wenn die Steuerung zum Beispiel auf älteren Maschinen diese Synchronisation nicht hergebe, seien diese Maschinen für die neuen Verfahren nicht nutzbar.
Wo die Bedingungen stimmen, sind allerdings große Vorteile zu erwarten. „Wir rechnen damit, dass wir die Bearbeitung dann vierzig Prozent schneller erledigen können“, sagt Luik. Und da die Maschinenstunden der Hauptkostentreiber seien, erschienen die neuen Verfahren auch für die unter Kostendruck stehenden Unternehmen der Medizintechnik sehr interessant.
Nicht nur für Titan interessant
Was die Zyklomed-Partner mit Titan getestet haben, lässt sich auch mit anderen Werkstoffen wie zum Beispiel Messing umsetzen. Damit schaffen die Verfahren neue Fertigungsmöglichkeiten in der Medizintechnik-Branche, aber auch darüber hinaus. (op)
Dieses Forschungs- und Entwicklungsprojekt wird durch das Bundesministerium für
Bildung und Forschung (BMBF) gefördert.
Weitere Informationen
Das Projekt Zyklomed baut auf Erfahrungen zum High-Speed-Wirbeln auf, die die Partner im Vorgängerprojekt „Gewinde“ erarbeitet haben. Die Sichtweise der Medizintechnik haben zwei assoziierte Partner im Projekt Zyklomed vertreten: die Dentaurum GmbH & Co. KG aus Ispringen und der Stryker-Konzern. Die Arbeiten liefen über drei Jahre und mussten während der Pandemie für längere Zeit ruhen. Im Jahr 2023 läuft das Projekt Zyklomed aus.
Drei neue Verfahren beschleunigen das Bearbeiten von Titan
Diese drei Verfahren wurden im Projekt Zyklomed entwickelt und erprobt.
- Beim Rotationsunrunddrehen wird ein rotierendes unrundes Werkzeug unter Lagekopplung am rotierenden Werkstück entlanggeführt. Die Drehzahlen sind hierbei in ein bestimmtes Verhältnis zueinander gebracht. Die unrunde Form bildet sich so innerhalb bestimmter Grenzen auf dem Bauteil ab.
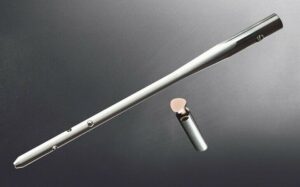
(Bild: Horn/Sauermann)
Geeignet für:
Das Verfahren bietet sich an für eine sehr produktive Fertigung von unrunden Außenkonturen. Durch das drehende Werkzeug verringert sich zudem die thermische Belastung der Werkzeugschneide, was für hohe Standzeiten sorgt. Mit dem Verfahren lassen sich auch konische Profilübergänge herstellen.
- Das Polygondrehen ist ein Verfahren, mit dem sich unrunde Außen- und Innenkonturen mit der Form einer Hypotrochoide fertigen lassen. Im Prozess stehen die parallelen Achsen des Werkstücks und des Werkzeugs um einen Achsabstand zueinander versetzt und sind unter Lagekopplung in ein bestimmtes Drehzahlverhältnis gebracht. Der Achsabstand, das Drehzahlverhältnis von Werkstück zu Werkzeug und der Flugkreis der Schneide definieren die Abmessung der Kontur. Ein Werkzeugsystem zum Polygondrehen ist individuell auf die jeweils herzustellende Kontur des Werkstücks abgestimmt.
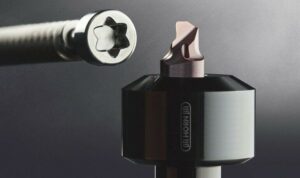
(Bild: Horn/Sauermann)
Geeignet für:
Auch dieser Prozess bietet die Möglichkeit, hypotrochoidische Außen- und Innenpolygone auf Drehmaschinen herzustellen.
- Das High-Speed-Wirbelfräsen (Dreh-Wirbelfräsen) ist ein nach Angaben der Entwickler sehr produktiver Prozess, bei dem ein oder zwei Zirkularfräser in einem bestimmten Winkel gegenüber dem Werkstück angestellt sind. Die Drehrichtungen der Fräser und des Werkstücks können gleich oder entgegengesetzt sein. Das Drehzahlverhältnis des Werkstücks zu den beiden Fräsern hängt von der Anzahl der Gewindegänge und der Anzahl der Schneiden der Fräser ab.
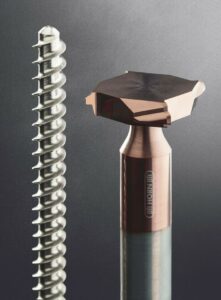
(Bild: Horn/Sauermann)
Geeignet für:
Mit dem High-Speed-Wirbelfräsen lassen sich Gewinde für Knochenschrauben herstellen – wirtschaftlich und erstmals auch mit echter variabler Steigung durch dynamische Änderung des Gewindeprofils.
Hier finden Sie mehr über: