Frau Dr. Hassberg, welches Ziel verfolgen Sie mit Ihrem Start-up Solios Diagnostics – und wie entstand die Idee?
Wir alle haben in der Corona-Pandemie häufig Kontakt mit Schnelltests gehabt – ich persönlich hatte als Medizinerin zu dieser Zeit viel mit Schultestungen zu tun. Die Lateral-Flow-Teststreifen, in denen sich die Probenflüssigkeit bewegt und in denen das Ergebnis zu sehen ist, wurden seit Jahren immer weiter entwickelt. Aber das Produkt an sich, das Gehäuse, die Art, wie man den Test benutzt, all das schien mir nicht mehr zeitgemäß. Schon nach kurzem Nachdenken gemeinsam mit meinem Vater, der ebenfalls Mediziner ist, gab es so viele Ideen, was man verändern könnte, um die Untersuchung an sich zu verbessern und um Müll zu vermeiden. Der Kern all dieser Überlegungen war dann, eine Plattform für Diagnostik-Tests entstehen zu lassen, die mit möglichst wenig Material auskommt und mit der man allerlei unterschiedliche Nachweise umsetzen kann. Um diese Idee für ein Diagnose-Kit umzusetzen, für die mein Vater das Patent hält, habe ich schließlich das Start-up Solios Diagnostics gegründet.
Was muss dafür neu entstehen, wo können Sie sich auf Bewährtes verlassen?
Unsere Aufgabe ist, das Konzept der Plattform zu entwickeln. Was muss sie bieten? Welche Funktionen muss sie haben? Wie sieht sie aus? Woraus stellen wir sie her? Für den Lateral-Flow-Test selbst gibt es dann Zulieferprodukte. Da wäre zunächst der Teststreifen, der in das Gehäuse eingelegt wird und für einen bestimmten Erregernachweis geeignet ist. Solche Teststreifen sind Standard. Dazu passend sind Pufferlösungen verfügbar, die meist der Teststreifenhersteller mit anbietet. Die Kapsel, in der die Pufferlösung aufbewahrt wird, ist wiederum unser Know-how. Auch die Probenahme-Einheiten sind Zulieferprodukte: Das können Abstrichstäbchen sein, wie man es vom Corona-Schnelltest kennt. Mit dieser Variante haben wir begonnen. Auch eine Art Spatel, mit dem man eine Stuhlprobe nehmen kann, ist denkbar. Andere Utensilien für einen Test an festem oder flüssigen Material kommen ebenfalls in Frage. Die Stuhl- und Blutprobenahme wollen als nächstes angehen. Je mehr Möglichkeiten wir in unsere Plattform integrieren können, desto größer ist die Chance, dass Hersteller von Diagnose-Kits sich für unsere Lösung entscheiden – und wir diese dann in großen Stückzahlen günstig herstellen können.
Wen haben Sie ins Boot geholt, um so ein Produkt auf die Beine zu stellen?
Wir haben ganz am Anfang im privaten Umfeld herumexperimentiert, mit alten Spritzenkörpern und einfachen 3D-Druck-Teilen. Man braucht aber ganz schnell professionelle Entwickler im Team. Die ersten Kontakte in dieser Richtung waren leider nicht zielführend. Das hatte zwei Gründe. Zum Einen hatte ich den Eindruck, dass die Ingenieure mir nicht richtig zugehört haben, nicht verstanden haben, um welche essentiellen Anforderungen es bei einem Diagnostikprodukt vor allem geht. Zum Anderen war mir von Anfang an klar, dass ich – wenn irgend möglich – ein nachhaltiges Produkt wollte, das auf biobasierten Kunststoffen beruht. Aber ich habe anfangs sehr oft gehört, dass das heute noch nicht ginge, dass das Projekt daran scheitern würde, dass der Markt dafür nicht bereit sei. Mein Überzeugung wollte ich dennoch nicht aufgeben. Und inzwischen habe ich mit den Spritzgussexperten von Sanner und dem Materialanbieter Biovox Partner gefunden, die das erforderliche Know-how haben und sich zutrauen, unsere Plattform technisch auszugestalten.
Mit biobasierten Kunststoffen nachhaltige IVD-Produkte spritzen
Warum sind Ihnen biobasierte Werkstoffe so wichtig?
Ein benutztes Diagnose-Kit muss, wie es das Gesetz vorschreibt, im Müll entsorgt werden, da es kontaminiertes Material enthalten kann. Wer heute so ein Produkt entwickelt, kann meiner Meinung nach den Aspekt der Nachhaltigkeit gar nicht mehr ignorieren. Wenn ich das Produkt am Ende aus Sicherheitsgründen verbrennen muss, wird CO2 freigesetzt. Also muss ich dafür sorgen, dass es erstens aus möglichst wenig Material besteht und dieses zweitens nicht aus Rohöl hergestellt wird. Nur dann kann die CO2-Bilanz für das spätere Produkt stimmen.
Welche Erfahrungen haben Sie bei der Entwicklung des Diagnose Kits mit den jetzigen Projektpartnern gemacht?
Was mich sehr freut, ist die professionelle Herangehensweise. Bei Sanner beispielsweise hat sich ganz schnell gezeigt, dass die Experten dort Erfahrungen mit Projekten wie meinem haben. Es gibt einen ausgearbeiteten Entwicklungsvertrag, klare Projektphasen, häufige Meetings, um die bisherigen Ergebnisse zu besprechen, zu sehen, was wir besser machen können. Parallel dazu entsteht die technische Dokumentation, die wir am Ende unbedingt brauchen werden. Und in wenigen Monaten hatten wir Prototypen, zunächst aus herkömmlichem Kunststoff, mit denen wir eine erste klinische Studie starten konnten. Nun geht es weiter damit, das Ganze auf einen biobasierten Werkstoff, auf PLA, zu übertragen. Da laufen dann auch Gespräche zwischen den Spritzgussexperten und dem Werkstoffspezialisten, zu denen ich als Medizinerin wenig beitragen kann. Aber der Professionalität der beiden Partner kann ich vertrauen, und so kommen wir Schritt für Schritt gut voran.
Was sehen Sie als mittelfristige Anwendungen für Ihre Diagnostik-Plattform?
Wir fangen mit Schleimhaut-Abstrichen an. Als nächster Schritt sind Analysen von Vollblut geplant. Was wir erreichen wollen, sind sehr genaue Testergebnisse, die sich schnell auf manuell-analogem Niveau erzielen lassen – also ohne Analyse im Labor, ohne komplexe Apps und Internet-Vernetzung mit Experten. Damit zum Beispiel ein Veterinärmediziner am Einsatzort Erreger nachweisen kann oder auch medizinisches Personal in Schwellenländern ohne Hürden zu Ergebnissen kommt.
Wie empfindlich können solche Test sein?
Man kommt damit schon relativ weit. Und auf lange Sicht gibt es eine weitere Perspektive: Die Plattform ist so konzipiert, dass wir darin auch Nukleinsäuren vervielfältigen können, über die so genannte Isotherme Amplifikation. Das Verfahren ähnelt dem der PCR, weist auch sehr geringe Erregemengen nach. Es kommt aber ohne die dafür erforderlichen Temperaturveränderungen aus, die man nur mit speziellen Laborgeräten erzeugen kann. Für unsere Plattform heißt das aber auch: Sie muss geschlossen sein. Sobald die Probe drin ist, kommt nichts mehr aus dem System heraus, auch kein amplifiziertes Material. Das ist wichtig, denn wenn das der Fall wäre, könnte das ausgetretene Material die Umgebung so stark kontaminieren, dass alle nachfolgenden Tests positiv ausfallen würden.
Wird die Plattform zu 100 Prozent aus biobasiertem Material bestehen?
Für alle Teile, die wir selbst herstellen, ist das das Ziel. Für Zulieferteile lässt sich das bisher noch nicht erreichen. Diese machen von der Masse her aber auch nur einen sehr kleinen Teil aus. Ich gehe heute von 95 Prozent biobasiertem Kunststoff aus.
Wird so eine Plattform teurer sein als ähnliche Produkte aus herkömmlichem Kunststoff?
Das hängt von den Stückzahlen ab, in denen wir die Plattform herstellen. Das Material an sich ist teurer als die herkömmlichen Werkstoffe. Für ein spezifisches Kit, mit dem beispielsweise Legionellen nachgewiesen werden sollen und von dem vielleicht 300 000 Stück jährlich gebraucht werden, würde sich das nicht rechnen. Aber unsere Plattform ist ja so konzipiert, dass das immer gleiche Gehäuse für verschiedene Teststreifen, Erreger und Probenahme-Werkzeuge verwendbar sein wird. Dann reden wir von Millionenstückzahlen – und damit fällt der Materialpreis kaum noch ins Gewicht.
Wie ist das Interesse am Diagnose Kit seitens der Pharma-Industrie?
Bei allen bisherigen Gesprächen bin ich auf offene Ohren gestoßen. Wobei es auch viel geholfen hat, dass ich schon zur Medica 2022 über einen Zufallskontakt sehr hochwertige Musterexemplare aus dem 3D-Drucker präsentieren konnte. Diese sahen einem fertigen Medizin- oder IVD-Produkt wirklich schon sehr ähnlich und wir konnten sogar die Funktion simulieren. Unter solchen Voraussetzungen fällt es leichter, mit einer Idee zu überzeugen.
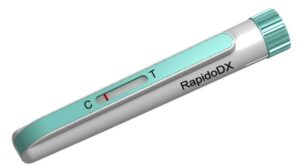
(Bild: Solios Diagnostics)
Was empfehlen Sie Entwicklern, die sich mit nachhaltigen Werkstoffen befassen wollen?
Sie sollten sich vor allem nicht entmutigen lassen. Wenn Sie auf Ansprechpartner treffen, die sagen, das haben wir noch nie gemacht und das geht nicht, brechen Sie das Gespräch ab und unterhalten Sie sich lieber mit Experten, die das gleiche Ziel wie Sie vor Augen haben und sich auskennen. Nur dann lässt sich einschätzen, wie man das erreicht, was man sich vorgenommen hat.
Wovor haben Sie bei der Umsetzung in den nächsten Monaten den größten Respekt?
Als Start-up steht die Frage der Finanzierung immer wieder im Raum. Und ich hoffe, dass wir genug Zeit haben werden, um die Entwicklungsarbeit in den Vordergrund stellen zu können – und nicht die Finanzierungsfragen zu viel Zeit in Anspruch nehmen. Wobei ich an dieser Stelle die Situation im Land Baden-Württemberg ausdrücklich loben möchte. Ohne die zahlreichen Fördermittel und Innovationsgutscheine und die geduldige und kompetente Beratung, die ich immer wieder bekommen habe, wären wir noch nicht da, wo wir jetzt schon sind.
Weitere Informationen
Über das Start-up Solios Diagnostics:
www.solios-dx.com
Wie das Projekt vorankommt
Die Entwicklung des IVD-Produktes für Probenmaterial, das mit einem Abstrich gewonnen werden kann, wird bis Mitte 2024 abgeschlossen sein. Die Finanzierung stammt, wie es für ein Startup typisch ist, aus verschiedenen Quellen. Gefördert werden die Arbeiten unter anderem durch das Pre-Seed-Programm der L-Bank Badenwürttemberg zusammen mit Business-Angels.
Die bisher erarbeiteten Konzepte und ersten Prototypen, die mit herkömmlichem Kunststoffen umgesetzt wurden, werden hinsichtlich funktioneller Anforderungen überarbeitet und dann auch in einer ersten biobasierten Version auf dem aktuellen Spritzgusswerkzeug gespritzt.
Für diese IVD-Plattform betreten die drei Partner Solios Diagnostics, Biovox und Sanner gemeinsam Neuland. Wie die Entwicklung des Diagnose-Kits voranschreitet, berichtet medizin&technik in den nächsten Monaten mit einer Reihe von Beiträgen.