Ein Fragezeichen im Gesicht. Das ist die spontane Reaktion darauf, wenn vom Spritzguss per Hand die Rede ist. Eine leistungsfähige manuelle Spritzgießmaschine? Großserien, Automatisierung, Anwendungen im Reinraum, Heißkanaltechnik, Zwei-Komponenten-Spritzguss – ja, klar. Aber das? Der manuelle Spritzguss ist natürlich nicht als Option für die Fertigung gedacht. In Entwicklungsabteilungen jedoch ist er vielfach im Einsatz.
In der Medizintechnik zum Beispiel: In dieser Branche bestehen viele medizintechnische Komponenten aus Hochleistungskunststoffen, die durch andere Materialien kaum zu ersetzen sind. Prototypen und Funktionsmuster lassen sich oft nur schwer im 3D-Druck realisieren, da die mechanischen Eigenschaften und die Oberflächenqualität nicht ausreichen. Der Spritzguss ist hier das bevorzugte Herstellungsverfahren, aufgrund der Kosten und Produktionsqualität.
„Eine ganze Reihe von Unternehmen aus der Medizintechnik nutzen die Holimaker-Geräte“, erklärt Udo Eckloff. Er ist in Schwäbisch Gmünd ansässig und vertritt den Maschinenbauer Holimaker in Deutschland und Österreich als Generalimporteur. „Seit der ersten Vorstellung der Maschinen in Deutschland auf der K-Messe 2021 wurden über 150 Maschinen verkauft.“
Dazu zählen laut Eckloff unter anderem Hersteller medizintechnischer Instrumente und Endoskope. Auch Entwicklungs- und Fertigungsdienstleister für Produkt- und Werkzeugentwicklung greifen auf die handbetriebenen Maschinen zurück. Spezialisten für Prototyping sowie Klein- und Vorserienfertigung im Spritzgussverfahren nutzen die Holipress ebenfalls seit mehreren Jahren und „haben teilweise sogar ihren Holimaker-Maschinenbestand erweitert“. Namentlich nennen darf Eckloff aus dieser Branche allerdings kein Unternehmen.
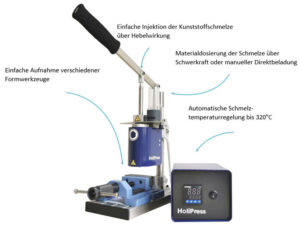
(Bild: Holimaker)
Qualität der Spritzgussteile: fast wie industriell gefertigt
Darüber, was sich mit den Maschinen tun lässt, gibt es allerdings etwas zu sagen. Die Anwender können ihren Auftraggebern oder ihrer Entwicklungsabteilung schnell Spritzgussteile in, wie Eckloff es nennt, „nahezu industriell gefertigter Qualität präsentieren“. So lassen sich Unzulänglichkeiten in der Werkstück- oder Werkzeugkonstruktion sowie nicht optimale Materialparameter früh erkennen. Auch wenn das häufige Zielmaterial PEEK aufgrund der hohen Schmelztemperaturen von über 320 °C nicht verarbeitet werden kann, lassen sich mit der Holipress andere Hochleistungskunststoffe wie PA6 und PA12, auch mit Füllmaterial, in Form bringen.
Funktionsmuster wie Griff-Halbschalen von chirurgischen Instrumenten, die in Kadavertests höheren Belastungen standhalten müssen, können mit einfachen Werkzeugen hergestellt werden. Sie bieten die Haptik und Funktion des späteren Serienprodukts und vermitteln potenziellen Kunden einen realistischen Eindruck des künftigen Produkts.
Ein weiteres Einsatzgebiet der Holipress findet sich im Bereich 2K-Werkstücke, die unter anderem auch in der Medizintechnik eingesetzt werden können. Hierzu laufen aktuell Tests bei der Plasmatreat GmbH in Steinhagen. Dabei wird untersucht, wie sich eine Plasmavorbehandlung auf neue so genannte Hart-Weichverbunde von verschiedenen Kunststoffmaterialien auswirkt. Ein Fokus dabei sind Recyclingmaterialien, um auch weitere zukünftige Anwendungsfelder abdecken zu können.
Forschungsinstitutionen wie das KUZ Leipzig, Institute der Max-Planck-Gesellschaft sowie Universitäten und Hochschulen in Köln, Bingen, Koblenz und im österreichischen Ferlach nutzen die Maschinen ebenfalls. Über Industrieunternehmen aus verschiedenen Branchen – wie Wegmann Automotive, Hansa, Geberit, Utz sowie Entwicklungsunternehmen wie Priomold, FES-Sportgeräte und Cool Hot Spots Technologies – darf Eckloff ebenfalls sprechen.
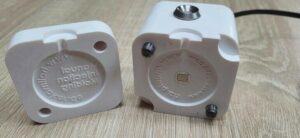
(Bild: Holimaker)
Einsatzmöglichkeiten fallen Messebesuchern laut Eckloff oft schon ein, wenn sie die Technik entdecken und eine Einführung bekommen. Ein Hersteller von Halterungen für Instrumenten-Sterilisationstrays kam beispielsweise auf die Idee, für Funktionsmodelle nicht das Zielmaterial, sondern zunächst 3D-gedruckte Spritzgießwerkzeuge und einfaches PP zu verwenden. Dadurch ließen sich die Halterungen so optimieren, dass das beste Sterilisationsergebnis erzielt wird. Erst nach der vollständigen Entwicklung folgt dann die industrielle Vorserienproduktion mit Stahlwerkzeugen und dem Zielmaterial PEEK auf herkömmlichen Spritzgießmaschinen. (op)
Über die Anfänge und Holimaker
Seit den 1960er Jahren sind manuelle Kolbenspritzgießmaschinen bekannt. Bereits 1954 entwickelten Arthur Hehl, der Gründer des Loßburger Spritzgießmaschinenherstellers Arburg, und seine Söhne Eugen und Karl die ersten Maschinen der Serie C. Damit stellten sie bis 1970 eigene Kunststoffprodukte her und verkauften auch die Maschine. Im Laufe der Zeit etablierte sich das Unternehmen mit perfektionierten und automatisierten Maschinen in der Spritzgusstechnologie.
Das bewährte Prinzip griff 2009 Aurélien Storky auf, der Gründer der Holimaker SAS in Frankreich. Er brachte erneut eine einfache, aber leistungsfähige manuelle Spritzgießmaschine auf den Markt, die Holipress. Sie eignet sich besonders für die Produktentwicklung, da sich damit mit geringem Aufwand und geringem Materialeinsatz seriennahe Kunststoffprodukte herstellen lassen.
Die Maschine verarbeitet Thermoplaste mit Schmelztemperaturen bis zu 320 °C, mit oder ohne Füllmaterial. Ihr Einspritzvolumen umfasst den Bereich von 16 cm³ bis 38 cm³.
Die Maschinen lassen sich mit beheizbaren Aluminiumwerkzeugen und 3D-gedruckten Werkzeugen aus speziellem Kunststoffmaterial sowie transparenten Werkzeugen vielfältig einsetzen – von Zugstäben über Prototypen bis hin zu Funktionsmustern und Kleinserien.
www.holimaker.fr, www.holimaker.de
Auf der Messe Fakuma:
Halle A3, Stand3211